La tecnologia de tall en daus de làmines, com a pas crític en el procés de fabricació de semiconductors, està directament relacionada amb el rendiment, el rendiment i els costos de producció dels xips.
#01 Antecedents i importància del tall en daus de neules
1.1 Definició de tall a daus de galeta
El tall en daus de les oblies (també conegut com a "scribing") és un pas essencial en la fabricació de semiconductors, destinat a dividir les oblies processades en múltiples matrius individuals. Aquestes matrius solen contenir la funcionalitat completa del circuit i són els components bàsics que s'utilitzen finalment en la producció de dispositius electrònics. A mesura que els dissenys de xips es tornen més complexos i les dimensions continuen reduint-se, els requisits de precisió i eficiència per a la tecnologia de tall en daus de les oblies són cada cop més estrictes.
En operacions pràctiques, el tall de làmines normalment utilitza eines d'alta precisió com ara fulles de diamant per garantir que cada dau romangui intacte i completament funcional. Els passos clau inclouen la preparació abans del tall, un control precís durant el procés de tall i la inspecció de qualitat després del tall.
Abans de tallar, l'oblia s'ha de marcar i posicionar per garantir trajectòries de tall precises. Durant el tall, els paràmetres com la pressió de l'eina i la velocitat s'han de controlar estrictament per evitar danys a l'oblia. Després del tall, es duen a terme inspeccions de qualitat exhaustives per garantir que cada xip compleixi els estàndards de rendiment.
Els principis fonamentals de la tecnologia de tall de làmines engloben no només la selecció de l'equip de tall i l'establiment dels paràmetres del procés, sinó també la influència de les propietats mecàniques i les característiques dels materials en la qualitat del tall. Per exemple, les làmines de silici dielèctriques de baixa k, a causa de les seves propietats mecàniques inferiors, són altament susceptibles a la concentració d'estrès durant el tall, cosa que provoca fallades com ara estelladura i esquerdes. La baixa duresa i fragilitat dels materials de baixa k els fan més propensos a danys estructurals sota força mecànica o estrès tèrmic, especialment durant el tall. El contacte entre l'eina i la superfície de la làmina, juntament amb les altes temperatures, pot exacerbar encara més la concentració d'estrès.
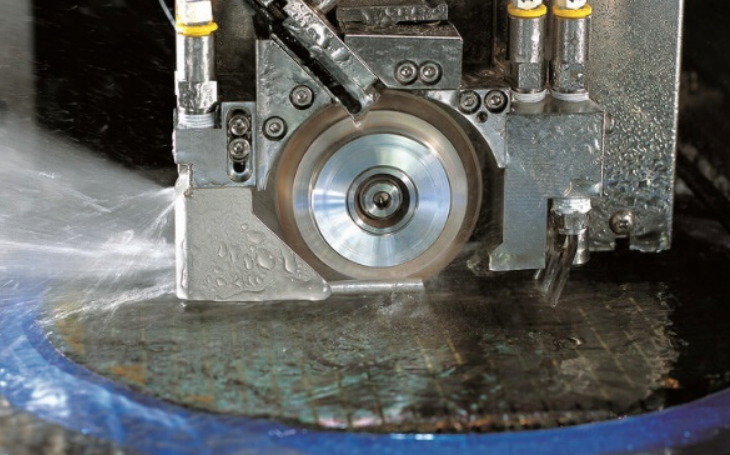
Amb els avenços en la ciència dels materials, la tecnologia de tall en daus d'oblies s'ha expandit més enllà dels semiconductors tradicionals basats en silici per incloure nous materials com el nitrur de gal·li (GaN). Aquests nous materials, a causa de la seva duresa i propietats estructurals, plantegen nous reptes per als processos de tall en daus, que requereixen millores addicionals en les eines i tècniques de tall.
Com a procés crític en la indústria dels semiconductors, el tall de làmines continua optimitzant-se en resposta a les demandes en evolució i els avenços tecnològics, establint les bases per a les futures tecnologies de microelectrònica i circuits integrats.
Les millores en la tecnologia de tall de làmines van més enllà del desenvolupament de materials i eines auxiliars. També abasten l'optimització de processos, millores en el rendiment dels equips i un control precís dels paràmetres de tall. Aquests avenços tenen com a objectiu garantir una alta precisió, eficiència i estabilitat en el procés de tall de làmines, satisfent la necessitat de la indústria dels semiconductors de dimensions més petites, una major integració i estructures de xips més complexes.
Àrea de Millora | Mesures específiques | Efectes |
Optimització de processos | - Millorar els preparatius inicials, com ara un posicionament més precís de les oblies i una planificació de la trajectòria. | - Reduir els errors de tall i millorar l'estabilitat. |
- Minimitzar els errors de tall i millorar l'estabilitat. | - Adopta mecanismes de monitorització i retroalimentació en temps real per ajustar la pressió, la velocitat i la temperatura de l'eina. | |
- Reduir les taxes de trencament de les oblies i millorar la qualitat del xip. | ||
Millora del rendiment dels equips | - Utilitzar sistemes mecànics d'alta precisió i tecnologia de control d'automatització avançada. | - Millora la precisió del tall i redueix el malbaratament de material. |
- Introduir tecnologia de tall per làser adequada per a oblies de materials d'alta duresa. | - Millorar l'eficiència de la producció i reduir els errors manuals. | |
- Augmentar l'automatització dels equips per a la supervisió i els ajustos automàtics. | ||
Control precís dels paràmetres | - Ajustar amb precisió paràmetres com la profunditat de tall, la velocitat, el tipus d'eina i els mètodes de refrigeració. | - Assegurar la integritat de la matriu i el rendiment elèctric. |
- Personalitza els paràmetres en funció del material, el gruix i l'estructura de la làmina. | - Augmentar les taxes de rendiment, reduir el malbaratament de materials i reduir els costos de producció. | |
Importància estratègica | - Explorar contínuament nous camins tecnològics, optimitzar processos i millorar les capacitats dels equips per satisfer les demandes del mercat. | - Millorar el rendiment i la fabricació de xips, donant suport al desenvolupament de nous materials i dissenys de xips avançats. |
1.2 La importància del tall en daus de les oblies
El tall de les oblies juga un paper fonamental en el procés de fabricació de semiconductors, i afecta directament els passos posteriors, així com la qualitat i el rendiment del producte final. La seva importància es pot detallar de la següent manera:
En primer lloc, la precisió i la consistència del tall en daus són clau per garantir el rendiment i la fiabilitat del xip. Durant la fabricació, les oblies se sotmeten a múltiples passos de processament per formar nombroses estructures de circuits complexos, que s'han de dividir amb precisió en xips individuals (dies). Si hi ha errors significatius en l'alineació o el tall durant el procés de tall en daus, els circuits es poden danyar, cosa que afecta la funcionalitat i la fiabilitat del xip. Per tant, la tecnologia de tall en daus d'alta precisió no només garanteix la integritat de cada xip, sinó que també evita danys als circuits interns, millorant la taxa de rendiment general.
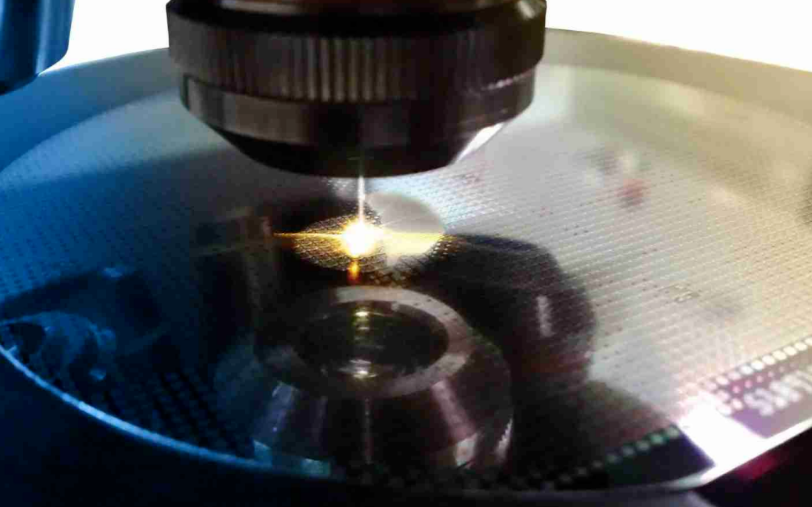
En segon lloc, el tall de làmines té un impacte significatiu en l'eficiència de la producció i el control de costos. Com a pas crucial en el procés de fabricació, la seva eficiència afecta directament el progrés dels passos posteriors. Optimitzant el procés de tall, augmentant els nivells d'automatització i millorant les velocitats de tall, es pot millorar considerablement l'eficiència de la producció general.
D'altra banda, el malbaratament de material durant el tall a daus és un factor crític en la gestió de costos. L'ús de tecnologies de tall a daus avançades no només redueix les pèrdues innecessàries de material durant el procés de tall, sinó que també augmenta l'ús de les oblies, reduint així els costos de producció.
Amb els avenços en la tecnologia dels semiconductors, els diàmetres de les oblies continuen augmentant i, en conseqüència, les densitats dels circuits augmenten, cosa que imposa una major demanda a la tecnologia de tall en daus. Les oblies més grans requereixen un control més precís de les trajectòries de tall, especialment en zones de circuits d'alta densitat, on fins i tot petites desviacions poden fer que diversos xips siguin defectuosos. A més, les oblies més grans impliquen més línies de tall i passos de procés més complexos, cosa que requereix més millores en la precisió, la consistència i l'eficiència de les tecnologies de tall en daus per afrontar aquests reptes.
1.3 Procés de tall en daus de galeta
El procés de tall de les oblees engloba tots els passos, des de la fase de preparació fins a la inspecció de qualitat final, i cada etapa és crítica per garantir la qualitat i el rendiment dels xips tallats a daus. A continuació, es mostra una explicació detallada de cada fase.
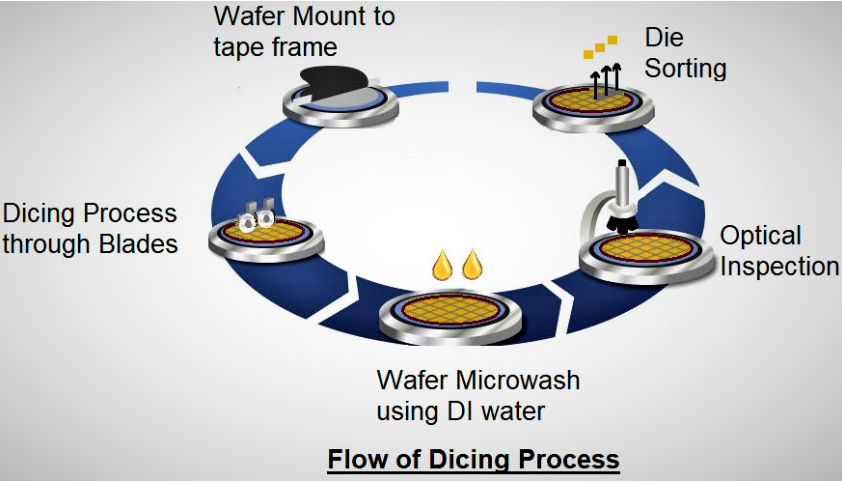
Fase | Descripció detallada |
Fase de preparació | -Neteja de galetesUtilitzeu aigua d'alta puresa i agents de neteja especialitzats, combinats amb un fregat ultrasònic o mecànic, per eliminar impureses, partícules i contaminants, garantint una superfície neta. -Posicionament precísUtilitzeu equips d'alta precisió per garantir que l'oblia es divideixi amb precisió al llarg dels camins de tall dissenyats. -Fixació de l'obliaFixeu l'oblia a un marc de cinta per mantenir l'estabilitat durant el tall, evitant danys per vibracions o moviment. |
Fase de tall | -Tall de fullesEmpren fulles recobertes de diamant giratòries d'alta velocitat per al tall físic, adequades per a materials a base de silici i rendibles. -Tall amb làserUtilitzen feixos làser d'alta energia per al tall sense contacte, ideal per a materials fràgils o d'alta duresa com el nitrur de gal·li, oferint una major precisió i menys pèrdua de material. -Noves tecnologiesIntroduir tecnologies de tall per làser i plasma per millorar encara més l'eficiència i la precisió, alhora que minimitza les zones afectades per la calor. |
Fase de neteja | - Utilitzeu aigua desionitzada (aigua DI) i agents de neteja especialitzats, combinats amb neteja per ultrasons o polvorització, per eliminar les restes i la pols generades durant el tall, evitant que els residus afectin els processos posteriors o el rendiment elèctric de la xip. L'aigua desionitzada (DI) d'alta puresa evita la introducció de nous contaminants, garantint un entorn de galeta net. |
Fase d'inspecció | -Inspecció òpticaUtilitzeu sistemes de detecció òptica combinats amb algoritmes d'IA per identificar ràpidament defectes, garantint que no hi hagi esquerdes ni estellades a les estelles tallades, millorant l'eficiència de la inspecció i reduint l'error humà. -Mesura de dimensions: Verifiqueu que les dimensions del xip compleixin les especificacions de disseny. -Proves de rendiment elèctricAssegurar que el rendiment elèctric dels xips crítics compleixi els estàndards, garantint la fiabilitat en aplicacions posteriors. |
Fase de classificació | - Utilitzeu braços robòtics o ventoses de buit per separar les fitxes qualificades del marc de la cinta i classificar-les automàticament en funció del rendiment, garantint l'eficiència i la flexibilitat de la producció alhora que milloreu la precisió. |
El procés de tall d'oblies implica la neteja, el posicionament, el tall, la neteja, la inspecció i la classificació d'oblies, i cada pas és crític. Amb els avenços en l'automatització, el tall per làser i les tecnologies d'inspecció d'IA, els sistemes moderns de tall d'oblies poden aconseguir una major precisió, velocitat i una menor pèrdua de material. En el futur, les noves tecnologies de tall com el làser i el plasma substituiran gradualment el tall tradicional amb fulles per satisfer les necessitats de dissenys de xips cada cop més complexos, impulsant encara més el desenvolupament dels processos de fabricació de semiconductors.
Tecnologia de tall de galeta i els seus principis
La imatge il·lustra tres tecnologies comunes de tall de galetes:Tall de fulles,Tall amb làser, iTall de plasma en dausA continuació es presenta una anàlisi detallada i una explicació suplementària d'aquestes tres tècniques:
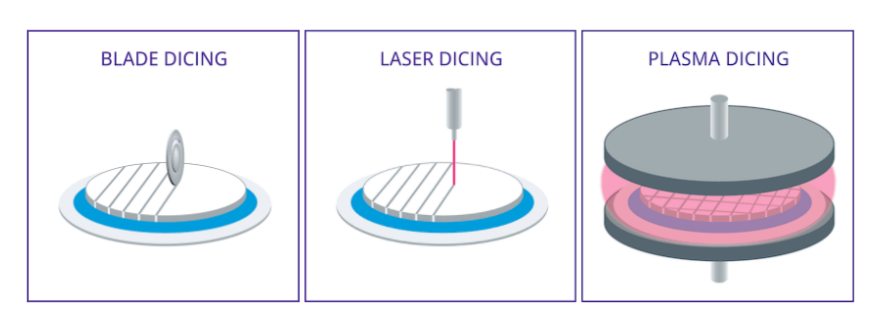
En la fabricació de semiconductors, el tall d'oblies és un pas crucial que requereix seleccionar el mètode de tall adequat en funció del gruix de l'oblia. El primer pas és determinar el gruix de l'oblia. Si el gruix de l'oblia supera les 100 micres, es pot triar el tall amb fulles com a mètode de tall. Si el tall amb fulles no és adequat, es pot utilitzar el mètode de tall per fractura, que inclou tant tècniques de tall per estampatge com de tall amb fulles.
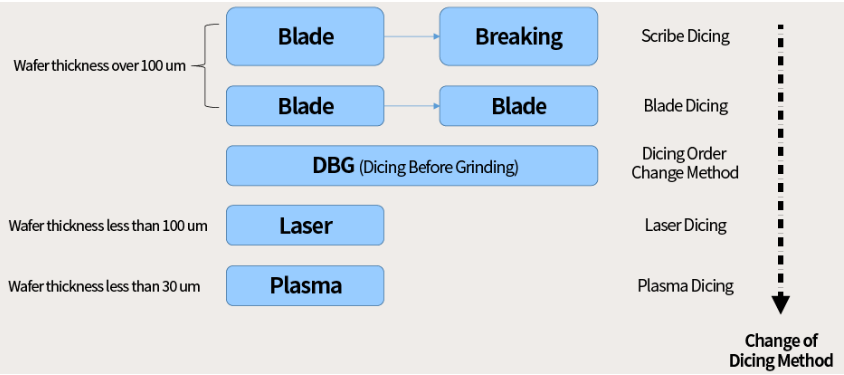
Quan el gruix de la làmina és d'entre 30 i 100 micres, es recomana el mètode DBG (Dice Before Grinding). En aquest cas, es pot triar el tall per marcar, el tall amb fulla o ajustar la seqüència de tall segons calgui per aconseguir els millors resultats.
Per a oblies ultraprimes amb un gruix inferior a 30 micres, el tall per làser esdevé el mètode preferit a causa de la seva capacitat de tallar oblies primes amb precisió sense causar danys excessius. Si el tall per làser no pot complir els requisits específics, es pot utilitzar el tall per plasma com a alternativa. Aquest diagrama de flux proporciona una via clara per a la presa de decisions per garantir que s'esculli la tecnologia de tall d'oblies més adequada en diferents condicions de gruix.
2.1 Tecnologia de tall mecànic
La tecnologia de tall mecànic és el mètode tradicional en el tall de les oblies. El principi bàsic és utilitzar una mola de diamant giratòria d'alta velocitat com a eina de tall per tallar l'oblia. L'equip clau inclou un eix amb coixinet d'aire, que acciona l'eina de la mola de diamant a altes velocitats per realitzar talls o ranurats precisos al llarg d'una trajectòria de tall predefinida. Aquesta tecnologia s'utilitza àmpliament a la indústria a causa del seu baix cost, alta eficiència i àmplia aplicabilitat.
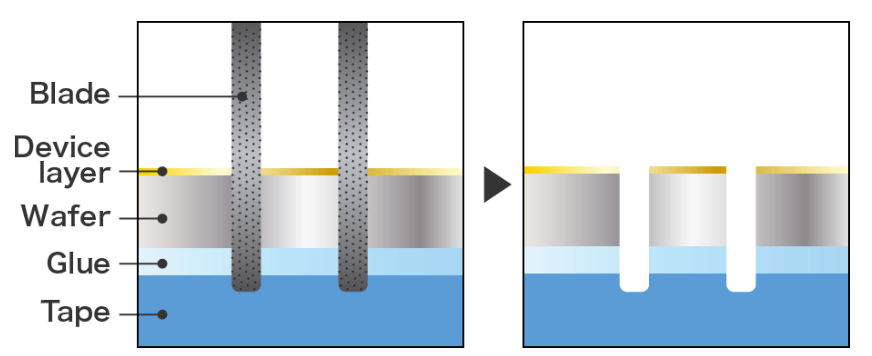
Avantatges
L'alta duresa i resistència al desgast de les eines de mòlta de diamant permeten que la tecnologia de tall mecànic s'adapti a les necessitats de tall de diversos materials d'oblies, ja siguin materials tradicionals basats en silici o semiconductors compostos més nous. El seu funcionament és senzill, amb requisits tècnics relativament baixos, cosa que promou encara més la seva popularitat en la producció en massa. A més, en comparació amb altres mètodes de tall com el tall per làser, el tall mecànic té costos més controlables, cosa que el fa adequat per a les necessitats de producció d'alt volum.
Limitacions
Malgrat els seus nombrosos avantatges, la tecnologia de tall mecànic també té limitacions. En primer lloc, a causa del contacte físic entre l'eina i l'oblea, la precisió del tall és relativament limitada, cosa que sovint provoca desviacions dimensionals que poden afectar la precisió de l'empaquetament i les proves posteriors dels xips. En segon lloc, durant el procés de tall mecànic es poden produir fàcilment defectes com ara estellades i esquerdes, cosa que no només afecta la taxa de rendiment, sinó que també pot tenir un impacte negatiu en la fiabilitat i la vida útil dels xips. El dany induït per l'estrès mecànic és particularment perjudicial per a la fabricació de xips d'alta densitat, especialment quan es tallen materials fràgils, on aquests problemes són més importants.
Millores tecnològiques
Per superar aquestes limitacions, els investigadors optimitzen contínuament el procés de tall mecànic. Les millores clau inclouen la millora del disseny i la selecció de materials de les moles per millorar la precisió i la durabilitat del tall. A més, l'optimització del disseny estructural i els sistemes de control dels equips de tall ha millorat encara més l'estabilitat i l'automatització del procés de tall. Aquests avenços redueixen els errors causats per les operacions humanes i milloren la consistència dels talls. La introducció de tecnologies avançades d'inspecció i control de qualitat per a la supervisió en temps real de les anomalies durant el procés de tall també ha millorat significativament la fiabilitat i el rendiment del tall.
Desenvolupament futur i noves tecnologies
Tot i que la tecnologia de tall mecànic encara ocupa una posició important en el tall de les oblies, les noves tecnologies de tall avancen ràpidament a mesura que evolucionen els processos de semiconductors. Per exemple, l'aplicació de la tecnologia de tall per làser tèrmic proporciona noves solucions als problemes de precisió i defectes en el tall mecànic. Aquest mètode de tall sense contacte redueix l'estrès físic a l'oblia, reduint significativament la incidència d'esquerdes i esquerdes, especialment quan es tallen materials més fràgils. En el futur, la integració de la tecnologia de tall mecànic amb les tècniques de tall emergents proporcionarà a la fabricació de semiconductors més opcions i flexibilitat, millorant encara més l'eficiència de fabricació i la qualitat dels xips.
En conclusió, tot i que la tecnologia de tall mecànic té certs inconvenients, les contínues millores tecnològiques i la seva integració amb noves tècniques de tall permeten que encara tingui un paper important en la fabricació de semiconductors i mantingui la seva competitivitat en processos futurs.
2.2 Tecnologia de tall per làser
La tecnologia de tall per làser, com a nou mètode de tall d'oblies, ha anat guanyant gradualment una atenció generalitzada a la indústria dels semiconductors a causa de la seva alta precisió, la manca de danys mecànics per contacte i les seves capacitats de tall ràpid. Aquesta tecnologia utilitza l'alta densitat d'energia i la capacitat d'enfocament d'un feix làser per crear una petita zona afectada per la calor a la superfície del material de l'oblia. Quan s'aplica el feix làser a l'oblia, la tensió tèrmica generada fa que el material es fracturi a la ubicació designada, aconseguint un tall precís.
Avantatges de la tecnologia de tall làser
• Alta precisióLa capacitat de posicionament precís del feix làser permet una precisió de tall a nivell de micres o fins i tot nanomètric, complint els requisits de la fabricació moderna de circuits integrats d'alta precisió i alta densitat.
• Sense contacte mecànicEl tall amb làser evita el contacte físic amb l'oblea, evitant problemes comuns en el tall mecànic, com ara l'esquerdament i l'esquerdament, millorant significativament el rendiment i la fiabilitat dels xips.
• Velocitat de tall ràpidaL'alta velocitat del tall per làser contribueix a augmentar l'eficiència de la producció, cosa que el fa especialment adequat per a escenaris de producció a gran escala i alta velocitat.
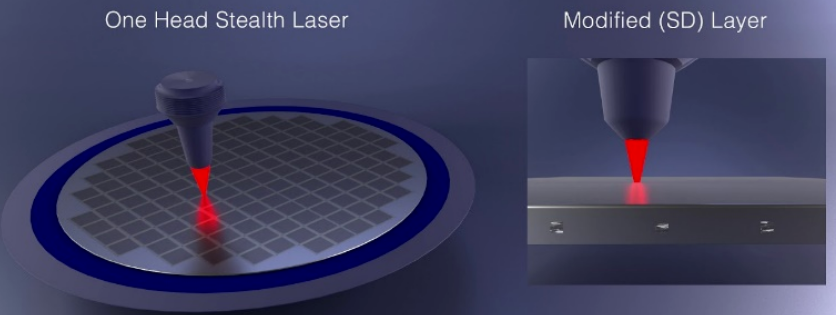
Reptes afrontats
• Cost elevat de l'equipamentLa inversió inicial en equips de tall per làser és elevada, cosa que representa una pressió econòmica, especialment per a les petites i mitjanes empreses de producció.
• Control de processos complexosEl tall per làser requereix un control precís de diversos paràmetres, com ara la densitat d'energia, la posició del focus i la velocitat de tall, cosa que fa que el procés sigui complex.
• Problemes de la zona afectada per la calorTot i que la naturalesa sense contacte del tall per làser redueix els danys mecànics, l'estrès tèrmic causat per la zona afectada per la calor (HAZ) pot afectar negativament les propietats del material de la làmina. Cal una optimització addicional del procés per minimitzar aquest efecte.
Direccions de millora tecnològica
Per abordar aquests reptes, els investigadors s'estan centrant en reduir els costos dels equips, millorar l'eficiència del tall i optimitzar el flux del procés.
• Làsers i sistemes òptics eficientsMitjançant el desenvolupament de làsers més eficients i sistemes òptics avançats, és possible reduir els costos dels equips alhora que millora la precisió i la velocitat de tall.
• Optimització dels paràmetres del procésS'està duent a terme una investigació en profunditat sobre la interacció entre els làsers i els materials de les oblies per millorar els processos que redueixen la zona afectada per la calor, millorant així la qualitat del tall.
• Sistemes de control intel·ligentsEl desenvolupament de tecnologies de control intel·ligent té com a objectiu automatitzar i optimitzar el procés de tall per làser, millorant-ne l'estabilitat i la consistència.
La tecnologia de tall per làser és particularment efectiva en oblies ultraprimes i en escenaris de tall d'alta precisió. A mesura que augmenten les mides de les oblies i les densitats dels circuits, els mètodes tradicionals de tall mecànic tenen dificultats per satisfer les demandes d'alta precisió i alta eficiència de la fabricació moderna de semiconductors. A causa dels seus avantatges únics, el tall per làser s'està convertint en la solució preferida en aquests camps.
Tot i que la tecnologia de tall per làser encara s'enfronta a reptes com ara els elevats costos dels equips i la complexitat del procés, els seus avantatges únics en alta precisió i danys sense contacte la converteixen en una direcció important per al desenvolupament en la fabricació de semiconductors. A mesura que la tecnologia làser i els sistemes de control intel·ligents continuen avançant, s'espera que el tall per làser millori encara més l'eficiència i la qualitat del tall de les oblies, impulsant el desenvolupament continu de la indústria dels semiconductors.
2.3 Tecnologia de tall per plasma
La tecnologia de tall per plasma, com a mètode emergent de tall per oblies, ha rebut una atenció significativa en els darrers anys. Aquesta tecnologia utilitza feixos de plasma d'alta energia per tallar oblies amb precisió controlant l'energia, la velocitat i la trajectòria de tall del feix de plasma, aconseguint resultats de tall òptims.
Principi de funcionament i avantatges
El procés de tall per plasma es basa en un feix de plasma d'alta temperatura i alta energia generat per l'equip. Aquest feix pot escalfar el material de la làmina fins al seu punt de fusió o vaporització en molt poc temps, cosa que permet un tall ràpid. En comparació amb el tall mecànic o làser tradicional, el tall per plasma és més ràpid i produeix una zona afectada per la calor més petita, cosa que redueix eficaçment l'aparició d'esquerdes i danys durant el tall.
En aplicacions pràctiques, la tecnologia de tall per plasma és particularment hàbil en la manipulació de oblies amb formes complexes. El seu feix de plasma ajustable i d'alta energia pot tallar fàcilment oblies de forma irregular amb alta precisió. Per tant, en la fabricació de microelectrònica, especialment en la producció personalitzada i en petits lots de xips d'alta gamma, aquesta tecnologia és molt prometedora per a un ús generalitzat.
Reptes i limitacions
Malgrat els molts avantatges de la tecnologia de tall per plasma, també s'enfronta a alguns reptes.
• Procés complexEl procés de tall per plasma és complex i requereix equips d'alta precisió i operadors experimentats per garantirprecisió i estabilitat en el tall.
• Control ambiental i seguretatLa naturalesa d'alta temperatura i alta energia del feix de plasma requereix mesures estrictes de control ambiental i seguretat, cosa que augmenta la complexitat i el cost de la implementació.
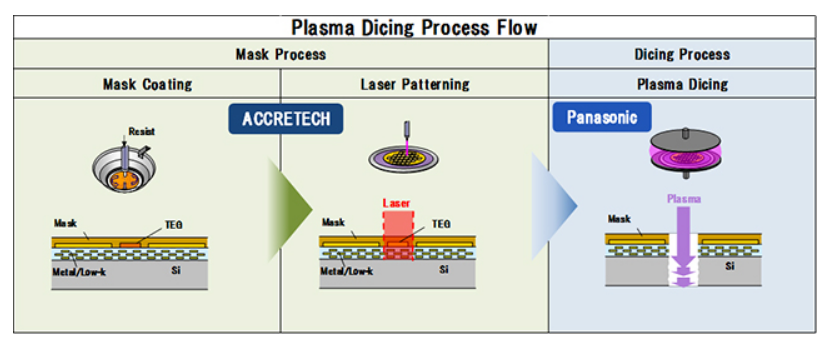
Direccions de desenvolupament futur
Amb els avenços tecnològics, s'espera que els reptes associats al tall per plasma es superin gradualment. Mitjançant el desenvolupament d'equips de tall més intel·ligents i estables, es pot reduir la dependència de les operacions manuals, millorant així l'eficiència de la producció. Al mateix temps, l'optimització dels paràmetres del procés i de l'entorn de tall ajudarà a reduir els riscos de seguretat i els costos operatius.
En la indústria dels semiconductors, les innovacions en la tecnologia de tall i tronxetatge d'oblies són crucials per impulsar el desenvolupament de la indústria. La tecnologia de tall per plasma, amb la seva alta precisió, eficiència i capacitat per manejar formes complexes d'oblies, ha emergit com un nou actor important en aquest camp. Tot i que encara hi ha alguns reptes, aquests problemes s'abordaran gradualment amb la innovació tecnològica contínua, aportant més possibilitats i oportunitats a la fabricació de semiconductors.
Les perspectives d'aplicació de la tecnologia de tall per plasma són àmplies i s'espera que en el futur tingui un paper més important en la fabricació de semiconductors. Mitjançant la innovació i l'optimització tecnològiques contínues, el tall per plasma no només abordarà els reptes existents, sinó que també es convertirà en un potent motor del creixement de la indústria dels semiconductors.
2.4 Qualitat de tall i factors d'influència
La qualitat del tall de les oblies és fonamental per a l'empaquetament posterior dels xips, les proves i el rendiment i la fiabilitat generals del producte final. Els problemes habituals que es troben durant el tall inclouen esquerdes, estellades i desviacions de tall. Aquests problemes estan influenciats per diversos factors que actuen conjuntament.
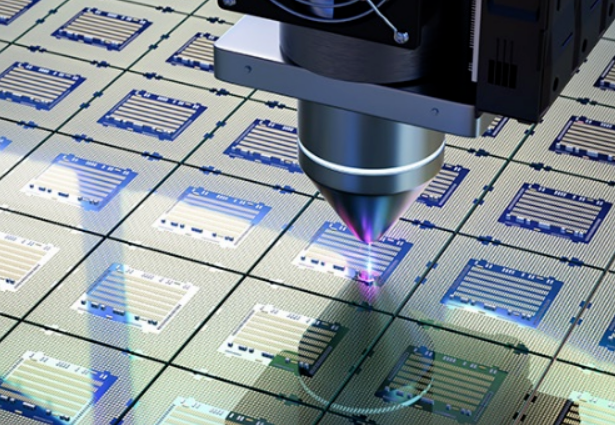
Categoria | Contingut | Impacte |
Paràmetres del procés | La velocitat de tall, la velocitat d'avanç i la profunditat de tall afecten directament l'estabilitat i la precisió del procés de tall. Una configuració incorrecta pot provocar una concentració d'estrès i una zona afectada per la calor excessiva, cosa que provoca esquerdes i estellades. Ajustar els paràmetres adequadament en funció del material de la làmina, el gruix i els requisits de tall és clau per aconseguir els resultats de tall desitjats. | Els paràmetres de procés adequats garanteixen un tall precís i redueixen el risc de defectes com ara esquerdes i estellades. |
Factors d'equipament i material | -Qualitat de la fullaEl material, la duresa i la resistència al desgast de la fulla influeixen en la suavitat del procés de tall i la planitud de la superfície de tall. Les fulles de mala qualitat augmenten la fricció i la tensió tèrmica, cosa que pot provocar esquerdes o estellades. Triar el material adequat de la fulla és crucial. -Rendiment del refrigerantEls refrigerants ajuden a reduir la temperatura de tall, minimitzar la fricció i eliminar les restes. Un refrigerant ineficaç pot provocar temperatures elevades i acumulació de restes, cosa que afecta la qualitat i l'eficiència del tall. Seleccionar refrigerants eficients i respectuosos amb el medi ambient és vital. | La qualitat de la fulla afecta la precisió i la suavitat del tall. Un refrigerant ineficaç pot resultar en una mala qualitat i eficiència de tall, cosa que posa de manifest la necessitat d'un ús òptim del refrigerant. |
Control de processos i inspecció de qualitat | -Control de processosMonitorització i ajust en temps real dels paràmetres clau de tall per garantir l'estabilitat i la consistència en el procés de tall. -Inspecció de qualitatLes comprovacions d'aspecte posteriors al tall, les mesures dimensionals i les proves de rendiment elèctric ajuden a identificar i abordar els problemes de qualitat amb rapidesa, millorant la precisió i la consistència del tall. | Un control de processos i una inspecció de qualitat adequats ajuden a garantir resultats de tall consistents i d'alta qualitat, així com a la detecció precoç de possibles problemes. |

Millora de la qualitat del tall
Millorar la qualitat del tall requereix un enfocament integral que tingui en compte els paràmetres del procés, la selecció d'equips i materials, el control i la inspecció del procés. Mitjançant el refinament continu de les tecnologies de tall i l'optimització dels mètodes de procés, es pot millorar encara més la precisió i l'estabilitat del tall de les oblies, proporcionant un suport tècnic més fiable per a la indústria de fabricació de semiconductors.
#03 Manipulació i proves posteriors al tall
3.1 Neteja i assecat
Els passos de neteja i assecat després del tall de les oblies són crítics per garantir la qualitat del xip i la bona progressió dels processos posteriors. Durant aquesta etapa, és essencial eliminar a fons les restes de silici, els residus de refrigerant i altres contaminants generats durant el tall. És igualment important assegurar-se que els xips no es facin malbé durant el procés de neteja i, després de l'assecat, assegurar-se que no quedi humitat a la superfície del xip per evitar problemes com la corrosió o la descàrrega electrostàtica.
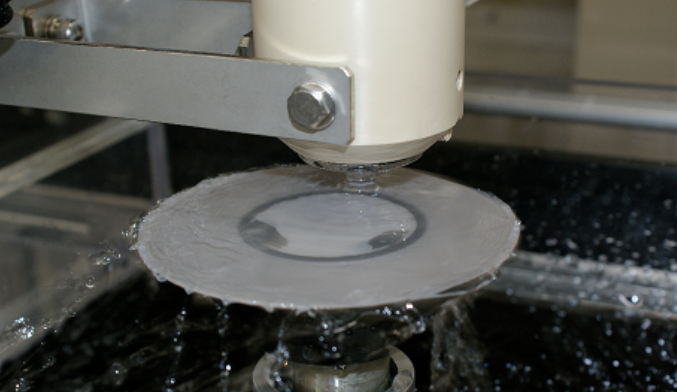
Manipulació posterior al tall: procés de neteja i assecat
Pas del procés | Contingut | Impacte |
Procés de neteja | -MètodeUtilitzeu agents de neteja especialitzats i aigua pura, combinats amb tècniques de raspallat ultrasònic o mecànic per a la neteja. | Garanteix l'eliminació completa de contaminants i evita danys a les estelles durant la neteja. |
-Selecció d'agents de netejaTrieu en funció del material de la làmina i del tipus de contaminant per garantir una neteja eficaç sense danyar el xip. | La selecció adequada de l'agent és clau per a una neteja eficaç i una protecció contra les encenalls. | |
-Control de paràmetresControleu estrictament la temperatura, el temps i la concentració de la solució de neteja per evitar problemes de qualitat causats per una neteja inadequada. | Els controls ajuden a evitar danys a l'oblea o deixar contaminants, garantint una qualitat constant. | |
Procés d'assecat | -Mètodes tradicionalsAssecat a l'aire natural i assecat a l'aire calent, que tenen una baixa eficiència i poden provocar acumulació d'electricitat estàtica. | Pot provocar temps d'assecat més lents i possibles problemes d'electricitat estàtica. |
-Tecnologies modernesUtilitzeu tecnologies avançades com l'assecat al buit i l'assecat per infrarojos per garantir que les encenalls s'assequin ràpidament i evitin els efectes nocius. | Procés d'assecat més ràpid i eficient, que redueix el risc de descàrrega estàtica o problemes relacionats amb la humitat. | |
Selecció i manteniment d'equips | -Selecció d'equipsLes màquines de neteja i assecat d'alt rendiment milloren l'eficiència del processament i controlen amb precisió els possibles problemes durant la manipulació. | Les màquines d'alta qualitat garanteixen un millor processament i redueixen la probabilitat d'errors durant la neteja i l'assecat. |
-Manteniment d'equipsLa inspecció i el manteniment regulars de l'equip asseguren que es mantingui en condicions òptimes de funcionament, garantint la qualitat de la ferritxa. | Un manteniment adequat evita fallades en els equips, garantint un processament fiable i d'alta qualitat. |
Neteja i assecat posterior al tall
Els passos de neteja i assecat després del tall de les oblies són processos complexos i delicats que requereixen una acurada consideració de múltiples factors per garantir el resultat final del processament. Mitjançant l'ús de mètodes científics i procediments rigorosos, és possible garantir que cada xip entri a les etapes posteriors d'embalatge i proves en condicions òptimes.
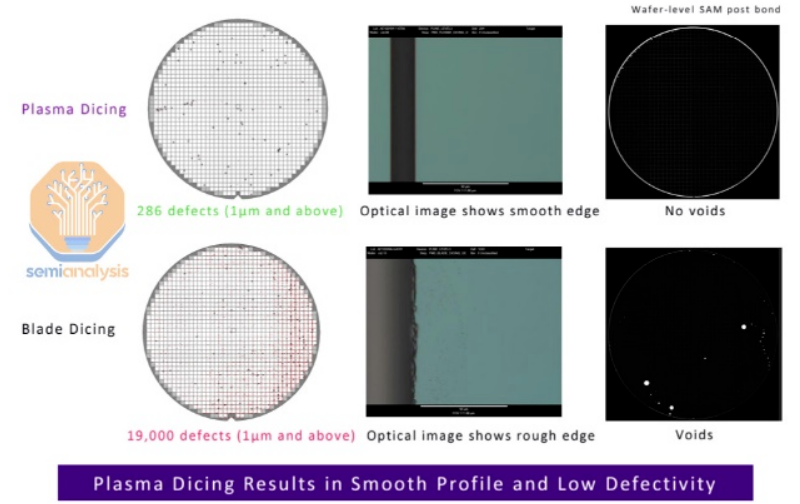
Inspecció i proves posteriors al tall
Pas | Contingut | Impacte |
Pas d'inspecció | 1.Inspecció visualUtilitzeu equips d'inspecció visual o automatitzats per comprovar si hi ha defectes visibles com ara esquerdes, estelles o contaminació a la superfície de la xip. Identifiqueu ràpidament les xips danyats físicament per evitar malbaratament. | Ajuda a identificar i eliminar les encenalls defectuoses al principi del procés, reduint la pèrdua de material. |
2.Mesura de la midaUtilitzeu dispositius de mesura de precisió per mesurar amb precisió les dimensions de les fitxes, garantint que la mida del tall compleixi les especificacions de disseny i evitant problemes de rendiment o dificultats d'embalatge. | Assegura que els xips estiguin dins dels límits de mida requerits, evitant la degradació del rendiment o problemes d'assemblatge. | |
3.Proves de rendiment elèctricAvaluar paràmetres elèctrics clau com la resistència, la capacitança i la inductància, per identificar xips no conformes i garantir que només els xips amb un rendiment qualificat passin a la següent etapa. | Garanteix que només els xips funcionals i amb un rendiment provat avancin en el procés, reduint el risc de fallada en etapes posteriors. | |
Pas de prova | 1.Proves funcionalsVerificar que la funcionalitat bàsica del xip funciona com està previst, identificant i eliminant els xips amb anomalies funcionals. | Assegura que els xips compleixin els requisits operatius bàsics abans de passar a etapes posteriors. |
2.Proves de fiabilitatAvaluar l'estabilitat del rendiment del xip en un ús prolongat o en entorns durs, que normalment impliquen l'envelliment a altes temperatures, proves a baixa temperatura i proves d'humitat per simular condicions extremes del món real. | Garanteix que els xips puguin funcionar de manera fiable en diverses condicions ambientals, millorant la longevitat i l'estabilitat del producte. | |
3.Proves de compatibilitatVerificar que el xip funciona correctament amb altres components o sistemes, assegurant-se que no hi hagi errors ni degradació del rendiment a causa d'incompatibilitat. | Garanteix un funcionament suau en aplicacions del món real evitant problemes de compatibilitat. |
3.3 Embalatge i emmagatzematge
Després del tall de les oblies, els xips són un resultat crucial del procés de fabricació de semiconductors, i les seves etapes d'embalatge i emmagatzematge són igualment importants. Unes mesures d'embalatge i emmagatzematge adequades són essencials no només per garantir la seguretat i l'estabilitat dels xips durant el transport i l'emmagatzematge, sinó també per proporcionar un suport sòlid per a les etapes posteriors de producció, proves i envasament.
Resum de les etapes d'inspecció i proves:
Els passos d'inspecció i prova dels xips després del tall de les oblies cobreixen una sèrie d'aspectes, com ara la inspecció visual, el mesurament de la mida, les proves de rendiment elèctric, les proves funcionals, les proves de fiabilitat i les proves de compatibilitat. Aquests passos estan interconnectats i complementaris, formant una barrera sòlida per garantir la qualitat i la fiabilitat del producte. Mitjançant procediments estrictes d'inspecció i prova, es poden identificar i resoldre ràpidament els possibles problemes, garantint que el producte final compleixi els requisits i les expectatives del client.
Aspecte | Contingut |
Mesures d'embalatge | 1.AntiestàticEls materials d'embalatge han de tenir excel·lents propietats antiestàtiques per evitar que l'electricitat estàtica danyi els dispositius o afecti el seu rendiment. |
2.Resistent a la humitatEls materials d'embalatge han de tenir una bona resistència a la humitat per evitar la corrosió i el deteriorament del rendiment elèctric causat per la humitat. | |
3.Resistent als copsEls materials d'embalatge han de proporcionar una absorció eficaç dels impactes per protegir les estelles de les vibracions i els impactes durant el transport. | |
Entorn d'emmagatzematge | 1.Control d'humitatControleu estrictament la humitat dins d'un rang adequat per evitar l'absorció d'humitat i la corrosió causades per un excés d'humitat o problemes estàtics causats per una baixa humitat. |
2.NetejaMantingueu un entorn d'emmagatzematge net per evitar la contaminació de les estelles per pols i impureses. | |
3.Control de temperaturaEstabliu un rang de temperatura raonable i manteniu l'estabilitat de la temperatura per evitar l'envelliment accelerat a causa de la calor excessiva o problemes de condensació causats per les baixes temperatures. | |
Inspecció regular | Inspeccioneu i avalueu regularment les fitxes emmagatzemades, mitjançant inspeccions visuals, mesures de mida i proves de rendiment elèctric per identificar i solucionar possibles problemes de manera oportuna. En funció del temps i les condicions d'emmagatzematge, planifiqueu l'ús de les fitxes per garantir que s'utilitzen en condicions òptimes. |
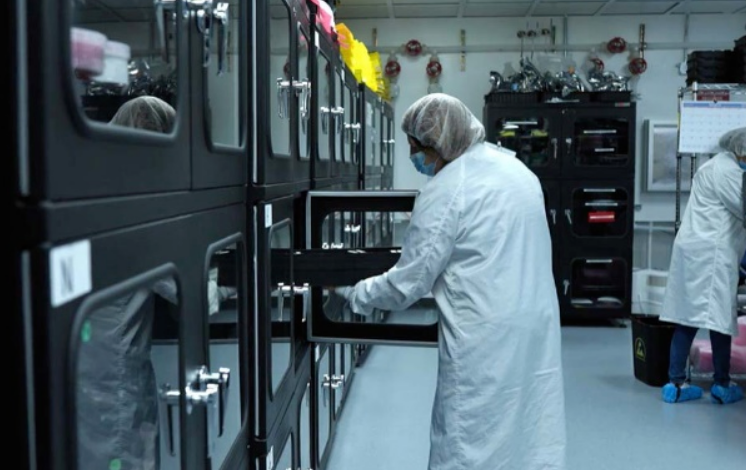
El problema de les microesquerdes i els danys durant el procés de tall de les oblies és un repte important en la fabricació de semiconductors. La tensió de tall és la causa principal d'aquest fenomen, ja que crea petites esquerdes i danys a la superfície de l'oblia, cosa que comporta un augment dels costos de fabricació i una disminució de la qualitat del producte.
Per abordar aquest repte, és crucial minimitzar l'estrès de tall i implementar tècniques, eines i condicions de tall optimitzades. Una atenció acurada a factors com el material de la fulla, la velocitat de tall, la pressió i els mètodes de refredament pot ajudar a reduir la formació de microesquerdes i millorar el rendiment general del procés. A més, la investigació contínua sobre tecnologies de tall més avançades, com ara el tall amb làser, està explorant maneres de mitigar encara més aquests problemes.
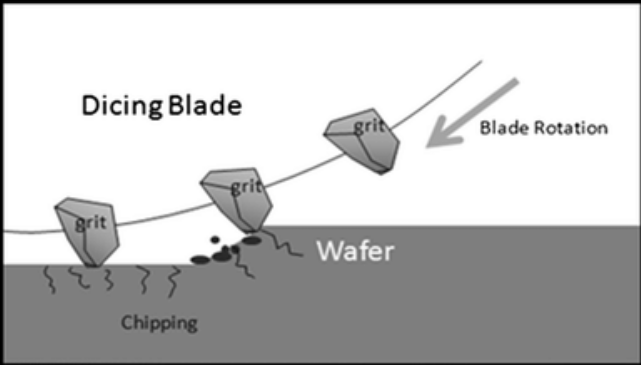
Com a material fràgil, les oblies són propenses a canvis estructurals interns quan se sotmeten a tensions mecàniques, tèrmiques o químiques, cosa que provoca la formació de microesquerdes. Tot i que aquestes esquerdes poden no ser immediatament perceptibles, poden expandir-se i causar danys més greus a mesura que avança el procés de fabricació. Aquest problema esdevé especialment problemàtic durant les etapes posteriors d'embalatge i proves, on les fluctuacions de temperatura i les tensions mecàniques addicionals poden fer que aquestes microesquerdes evolucionin cap a fractures visibles, cosa que pot provocar la fallada del xip.
Per mitigar aquest risc, és essencial controlar el procés de tall acuradament optimitzant paràmetres com la velocitat de tall, la pressió i la temperatura. L'ús de mètodes de tall menys agressius, com el tallat amb làser, pot reduir l'estrès mecànic a l'oblia i minimitzar la formació de microesquerdes. A més, la implementació de mètodes d'inspecció avançats com l'escaneig infraroig o les imatges de raigs X durant el procés de tall de l'oblia pot ajudar a detectar aquestes esquerdes en fase inicial abans que causin més danys.
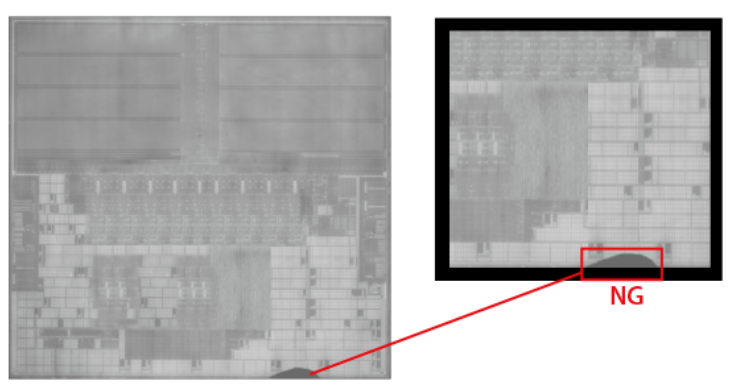
El dany a la superfície de l'oblia és una preocupació important en el procés de tall en daus, ja que pot tenir un impacte directe en el rendiment i la fiabilitat del xip. Aquests danys poden ser causats per un ús inadequat d'eines de tall, paràmetres de tall incorrectes o defectes de material inherents a la pròpia oblia. Independentment de la causa, aquests danys poden provocar alteracions en la resistència elèctrica o la capacitància del circuit, afectant el rendiment general.
Per abordar aquests problemes, s'estan explorant dues estratègies clau:
1. Optimització d'eines de tall i paràmetresSi s'utilitzen fulles més afilades, s'ajusta la velocitat de tall i es modifica la profunditat de tall, es pot minimitzar la concentració d'estrès durant el procés de tall, reduint així el potencial de danys.
2. Exploració de noves tecnologies de tallTècniques avançades com el tall per làser i el tall per plasma ofereixen una precisió millorada alhora que redueixen potencialment el nivell de danys infligits a l'oblia. Aquestes tecnologies s'estan estudiant per trobar maneres d'aconseguir una alta precisió de tall alhora que minimitzen l'estrès tèrmic i mecànic a l'oblia.
Àrea d'impacte tèrmic i els seus efectes sobre el rendiment
En processos de tall tèrmic com el tall per làser i plasma, les altes temperatures creen inevitablement una zona d'impacte tèrmic a la superfície de la làmina. Aquesta zona, on el gradient de temperatura és significatiu, pot alterar les propietats del material, afectant el rendiment final del xip.
Impacte de la Zona Afectada Tèrmicament (TAZ):
Canvis en l'estructura cristal·linaA altes temperatures, els àtoms del material de la làmina es poden reorganitzar, causant distorsions en l'estructura cristal·lina. Aquesta distorsió debilita el material, reduint la seva resistència mecànica i estabilitat, cosa que augmenta el risc de fallada del xip durant l'ús.
Canvis en les propietats elèctriquesLes altes temperatures poden alterar la concentració i la mobilitat dels portadors en els materials semiconductors, afectant la conductivitat elèctrica i l'eficiència de transmissió de corrent del xip. Aquests canvis poden provocar una disminució del rendiment del xip, cosa que podria fer-lo inadequat per al seu propòsit previst.
Per mitigar aquests efectes, controlar la temperatura durant el tall, optimitzar els paràmetres de tall i explorar mètodes com els dolls de refrigeració o els tractaments de postprocessament són estratègies essencials per reduir l'abast de l'impacte tèrmic i mantenir la integritat del material.
En general, tant les microesquerdes com les zones d'impacte tèrmic són reptes crucials en la tecnologia de tall de làmines. Caldrà continuar la recerca, juntament amb els avenços tecnològics i les mesures de control de qualitat, per millorar la qualitat dels productes semiconductors i augmentar la seva competitivitat al mercat.
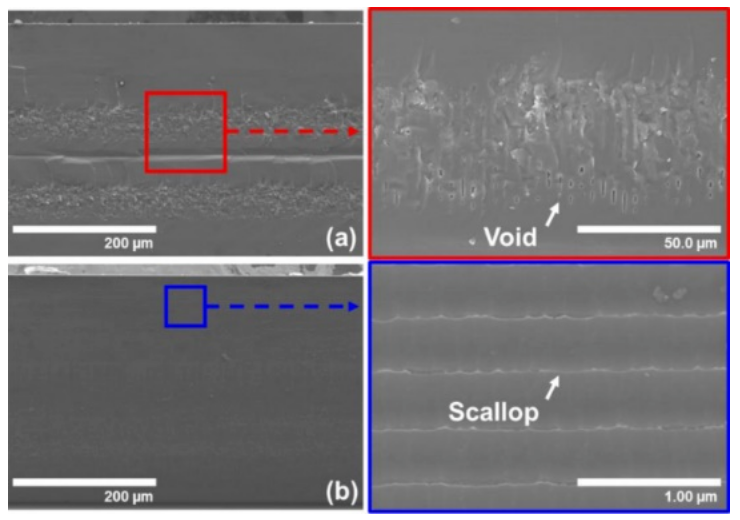
Mesures per controlar la zona d'impacte tèrmic:
Optimització dels paràmetres del procés de tallReduir la velocitat i la potència de tall pot minimitzar eficaçment la mida de la zona d'impacte tèrmic (TAZ). Això ajuda a controlar la quantitat de calor generada durant el procés de tall, que afecta directament les propietats del material de l'oblea.
Tecnologies de refrigeració avançadesL'aplicació de tecnologies com la refrigeració amb nitrogen líquid i la refrigeració microfluídica pot limitar significativament l'abast de la zona d'impacte tèrmic. Aquests mètodes de refrigeració ajuden a dissipar la calor de manera més eficient, preservant així les propietats del material de la làmina i minimitzant els danys tèrmics.
Selecció de materialsEls investigadors estan explorant nous materials, com ara els nanotubs de carboni i el grafè, que posseeixen una excel·lent conductivitat tèrmica i resistència mecànica. Aquests materials poden reduir la zona d'impacte tèrmic alhora que milloren el rendiment general dels xips.
En resum, tot i que la zona d'impacte tèrmic és una conseqüència inevitable de les tecnologies de tall tèrmic, es pot controlar eficaçment mitjançant tècniques de processament optimitzades i selecció de materials. És probable que la recerca futura se centri en l'afinament i l'automatització dels processos de tall tèrmic per aconseguir un tall de les oblies més eficient i precís.

Estratègia d'equilibri:
Aconseguir l'equilibri òptim entre el rendiment de les oblies i l'eficiència de la producció és un repte continu en la tecnologia de tall de les oblies. Els fabricants han de tenir en compte múltiples factors, com ara la demanda del mercat, els costos de producció i la qualitat del producte, per desenvolupar una estratègia de producció i uns paràmetres de procés racionals. Al mateix temps, la introducció d'equips de tall avançats, la millora de les habilitats dels operadors i la millora del control de qualitat de les matèries primeres són essencials per mantenir o fins i tot millorar el rendiment alhora que augmenten l'eficiència de la producció.
Reptes i oportunitats futurs:
Amb l'avanç de la tecnologia dels semiconductors, el tall d'oblies s'enfronta a nous reptes i oportunitats. A mesura que la mida dels xips es redueix i la integració augmenta, les demandes de precisió i qualitat del tall creixen significativament. Simultàniament, les tecnologies emergents proporcionen noves idees per al desenvolupament de tècniques de tall d'oblies. Els fabricants han d'estar atents a la dinàmica del mercat i a les tendències tecnològiques, ajustant i optimitzant contínuament les estratègies de producció i els paràmetres del procés per satisfer els canvis del mercat i les demandes tecnològiques.
En conclusió, integrant consideracions sobre la demanda del mercat, els costos de producció i la qualitat del producte, i introduint equips i tecnologia avançats, millorant les habilitats dels operadors i enfortint el control de les matèries primeres, els fabricants poden aconseguir el millor equilibri entre el rendiment de les oblies i l'eficiència de la producció durant el tall de les oblies, cosa que porta a una producció eficient i d'alta qualitat de productes semiconductors.
Perspectives de futur:
Amb els ràpids avenços tecnològics, la tecnologia dels semiconductors està progressant a un ritme sense precedents. Com a pas crític en la fabricació de semiconductors, la tecnologia de tall de làmines està preparada per a nous desenvolupaments emocionants. De cara al futur, s'espera que la tecnologia de tall de làmines aconsegueixi millores significatives en precisió, eficiència i cost, injectant nova vitalitat al creixement continu de la indústria dels semiconductors.
Augment de la precisió:
En la recerca d'una major precisió, la tecnologia de tall de blisters superarà contínuament els límits dels processos existents. Estudiant en profunditat els mecanismes físics i químics del procés de tall i controlant amb precisió els paràmetres de tall, s'aconseguiran resultats de tall més precisos per satisfer els requisits de disseny de circuits cada cop més complexos. A més, l'exploració de nous materials i mètodes de tall millorarà significativament el rendiment i la qualitat.
Millora de l'eficiència:
Els nous equips de tall de làmines se centraran en un disseny intel·ligent i automatitzat. La introducció de sistemes de control i algoritmes avançats permetrà als equips ajustar automàticament els paràmetres de tall per adaptar-se a diferents materials i requisits de disseny, millorant així significativament l'eficiència de la producció. Les innovacions com la tecnologia de tall de múltiples làmines i els sistemes de substitució ràpida de les fulles tindran un paper crucial en la millora de l'eficiència.
Reducció de costos:
La reducció de costos és una direcció clau per al desenvolupament de la tecnologia de tall de plaques. A mesura que es desenvolupen nous materials i mètodes de tall, s'espera que els costos dels equips i les despeses de manteniment es controlin de manera efectiva. A més, l'optimització dels processos de producció i la reducció de les taxes de ferralla reduiran encara més els residus durant la fabricació, cosa que comportarà una disminució dels costos de producció generals.
Fabricació intel·ligent i IoT:
La integració de la fabricació intel·ligent i les tecnologies de la Internet de les Coses (IoT) portarà canvis transformadors a la tecnologia de tall de làmines. Mitjançant la interconnectivitat i l'intercanvi de dades entre dispositius, es pot monitoritzar i optimitzar cada pas del procés de producció en temps real. Això no només millora l'eficiència de la producció i la qualitat del producte, sinó que també proporciona a les empreses una previsió de mercat i un suport en la presa de decisions més precisos.
En el futur, la tecnologia de tall de làmines farà avenços notables en precisió, eficiència i cost. Aquests avenços impulsaran el desenvolupament continu de la indústria dels semiconductors i aportaran més innovacions tecnològiques i comoditats a la societat humana.
Data de publicació: 19 de novembre de 2024